Power Curbers Companies has been honored with the 2024 Continuous Improvement Award in recognition of its remarkable commitment to enhancing manufacturing processes and driving organizational excellence. The journey began with a thorough evaluation of existing processes to identify inefficiencies and areas for improvement. Understanding the pivotal role of its workforce in fostering continuous improvement, Power Curbers implemented comprehensive Lean training programs, instilling foundational principles and practical tools such as 6S, Kaizen, Value Stream Mapping, one-piece flow, and Kanban systems. These initiatives aimed to cultivate a culture of continuous improvement across all levels of the organization, fostering a proactive approach to problem-solving and operational enhancement.
For 71 years, family-owned Power Curbers has specialized in manufacturing curb and gutter machines, which are large and heavy construction machines comparable to bulldozers. These machines are designed to accommodate forms or molds, allowing for the creation of various structures such as curbs, gutters, and sidewalk barrier walls commonly seen along highways and interstates.
Power Curbers customers are divided into three segments. The first consists of small contractors who operate independently, like mom-and-pop businesses, handling all aspects of their projects. The second segment comprises general concrete contractors and medium-sized companies engaged in various concrete-related projects such as floors, buildings, fountains, and tilt-up walls, for whom this machine is just one of many tools. The third group includes highway contractors or site prep contractors responsible for tasks like preparing mall parking lots or subdivisions for roads.
“Twenty-two years ago, we embarked on our lean journey due to frustrations with our quality and efficiency. Recognizing the need for improvement, we sought outside help and visited other companies that were successfully implementing lean practices. After observing and learning from their experiences, we began implementing lean principles, starting with our manufacturing processes. Over time, we extended these practices to other business areas, including lean accounting, striving to apply lean principles comprehensively throughout our organization,” stated Stephen Bullock, president and CEO of Power Curbers.
Instilling a culture of continuous improvement posed significant challenges. It necessitated assertive leadership from the top to outline the path forward. Analogies about getting the right individuals onboard and ensuring they’re in suitable roles were frequently used, recognizing that not everyone would embrace the change. “It took concerted efforts throughout the first year to embed this mindset across the organization and garner genuine buy-in. The objective was clear: embracing continuous improvement wouldn’t jeopardize job security but enhance our collective success,” stated Bullock.
Implementing Lean tools and practices was instrumental in addressing specific inefficiencies and promoting a more organized, efficient, and safe work environment. For instance, adopting the 6S methodology significantly improved productivity and safety by organizing and standardizing the workplace, reducing search times, and minimizing accidents on the shop floor. Additionally, the company embarked on targeted Kaizen events, such as the “Plan for Every Part” and “6S in the Raw Steel Supermarket Rack,” which focused on problem identification, objective setting, team formation, and solution development. These events led to immediate operational improvements, empowering employees and reducing lead times by 30%, enhancing on-time delivery rates and increasing sales.
Power Curbers has come a long way in embracing continuous improvement processes. Previously, there was a hero mentality, where errors were made and individuals had to work overtime to rectify them. Whether rushing parts to customers or addressing machine malfunctions, it was often a chaotic race against time. However, with lean principles, operations have become more streamlined. “Our inventory management underwent a significant overhaul. We realized the cost implications of excess inventory sitting idle on shelves and devised a coherent system to optimize inventory levels. Looking back, the transformation is remarkable. What was once a cluttered workspace with scattered parts is now organized with designated areas and shadow boards for easy access to tools and materials. This shift has improved efficiency and reflects our commitment to continuous improvement and operational excellence,” proclaimed Bullock.
Power Curbers documented and standardized the new rack layout and min/max inventory management process to ensure the sustainability of the improvements. The company implemented a visual management system to enhance material identification, improved inventory management to eliminate shortages, and optimized material organization for easy access and cycle counting. Other Lean projects executed by Power Curbers, such as the 6S Event at Shipping and Receiving and the Welding Area Event, further underscored the company’s commitment to continuous improvement and yielded substantial savings to the bottom line.
Implementing Six Sigma, Kaizen, and lean manufacturing practices has significantly enhanced Power Curbers’ operations. One of the critical strategies they employ is just-in-time delivery for our parts, which has proven exceptionally beneficial. “The just-in-time approach allows us to streamline our production process, from receiving raw materials to shipping the finished product, ensuring optimal cash flow. By adopting single-piece flow instead of batch processing, we avoid the accumulation of excess inventory and minimize the time between production and payment. This shift has greatly improved our cash flow and overall operational efficiency, contributing significantly to our success,” said Bullock.
Bullock says embarking on a journey of continuous improvement in manufacturing requires a candid self-assessment to pinpoint areas for enhancement. This introspection lays the groundwork for identifying weaknesses and areas ripe for improvement. Equally vital is the active involvement and commitment of company leadership. “Without your leadership’s steadfast determination, navigating the inevitable challenges and resistance within the workforce becomes daunting. It’s crucial to secure early victories to bolster momentum and rally support, especially among those employees who may initially be hesitant or resistant to change. By achieving tangible successes early on, the organization can effectively sway most of the workforce towards embracing the continuous improvement initiative, paving the way for lasting positive transformation,” stated Bullock.
The Continuous Improvement Award recognizes organizations that exemplify continuous improvement methodologies to drive organizational behaviors aligned with a detailed action plan and timeline. Power Curbers’ dedication to implementing Lean practices, fostering employee engagement, and achieving tangible operational improvements exemplifies its commitment to excellence. It sets a benchmark for continuous improvement in the manufacturing industry. “We are thrilled to receive the 2024 Continuous Improvement Leadership Award. The news was a fantastic surprise, and we couldn’t be more excited. We gratefully accept this prestigious honor for all our dedicated associates and sincerely appreciate the recognition. It reaffirms our commitment to continuous improvement and inspires us to push further towards excellence in everything we do,” proclaimed Bullock.
Power Curbers Awarded the 2024 Continuous Improvement Award
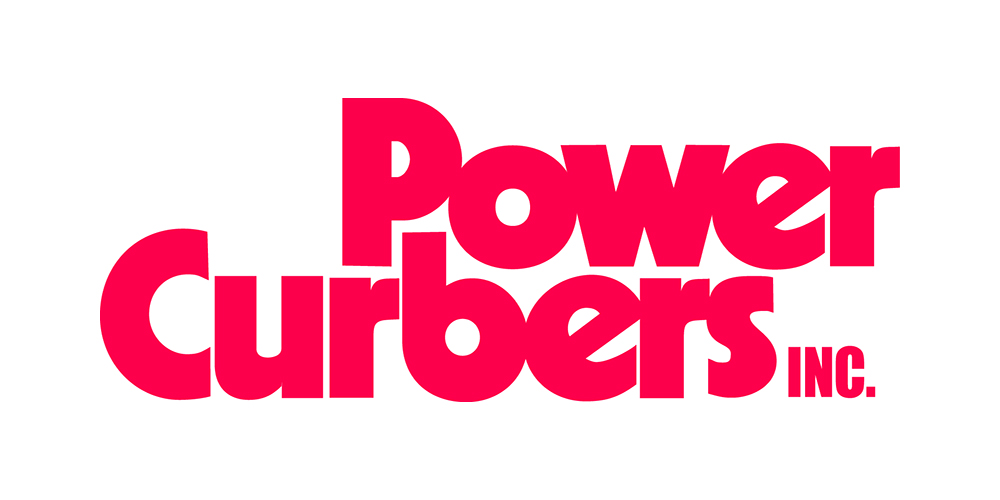